-
最近の投稿
アーカイブ
カテゴリー
投稿日カレンダー
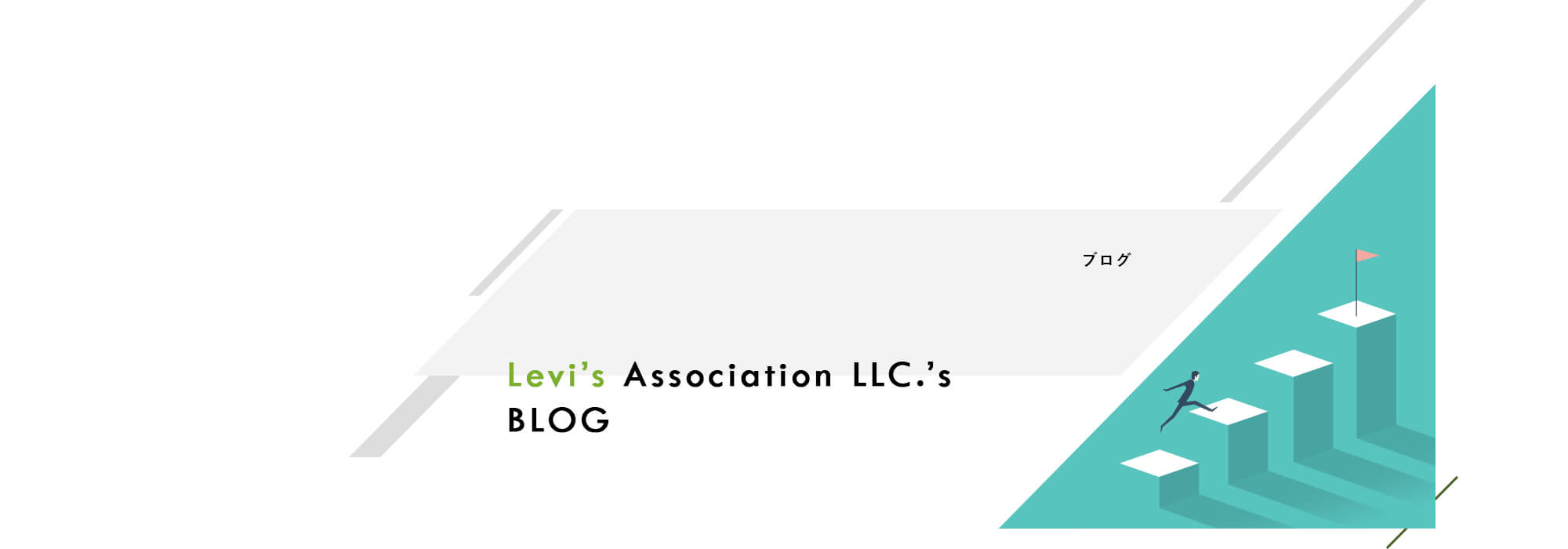
皆さんこんにちは!
合同会社Levi’s商会、更新担当の中西です。
さて
~メンテナンスと交換時期~
ということで、溶接構造物のメンテナンス方法・交換が必要となる劣化の兆候・長持ちさせるポイントについて詳しく解説 します♪
溶接工事で作られた構造物や設備は、耐久性が高く、長期間使用できる ことが特徴ですが、定期的なメンテナンスを行わなければ劣化が進行し、安全性が低下するリスクがあります。
また、溶接部に発生するひび割れ・腐食・応力集中による金属疲労 などの問題は、放置すると重大な事故につながる可能性があります。
では、溶接物の寿命を延ばし、安全に使用するためには、どのようなメンテナンスが必要なのでしょうか?また、交換時期はどのように判断すればよいのでしょうか?
溶接構造物は、建築物・橋梁・配管・機械部品・プラント設備など重要な役割を担っている ため、劣化を放置すると崩壊や破損のリスクが高まる 可能性があります。
✅ 例:橋梁の溶接部が腐食し、強度が低下すると、崩落事故につながる
✅ 例:プラント設備の配管が劣化すると、ガス漏れや爆発の原因になる
溶接部の劣化を早期に発見し、適切に補修すれば、大規模な修理や交換を防ぎ、コストを削減することが可能 です。
✅ 軽微なひび割れを補修せず放置すると、大きな亀裂に発展し、補修費用が数倍に増加する
✅ 定期メンテナンスを行えば、長期的に設備の寿命を延ばし、交換頻度を減らせる
溶接を用いた構造物は、定期的な検査が義務付けられているケースが多い です。例えば、
こうした法的な点検を怠ると、事故発生時に責任が問われることもあるため、適切なメンテナンスが不可欠 です。
溶接物の耐久性を損なう主な原因には、腐食・ひび割れ・金属疲労・応力集中 などがあります。これらの兆候を早期に発見することが重要です。
原因:
点検ポイント:
✅ サビが発生していないか?(特に溶接部周辺)
✅ 腐食による穴あきや表面の荒れがないか?
✅ 防錆塗装やメッキが剥がれていないか?
対策:
原因:
点検ポイント:
✅ 溶接部に細かいひび割れが発生していないか?
✅ 金属表面の異常(剥離や変色)がないか?
✅ 振動や荷重がかかる部分にひびが広がっていないか?
対策:
原因:
点検ポイント:
✅ 定期点検で溶接部の微細なひびを確認する
✅ 振動が多い部分のボルトや接合部の緩みをチェックする
対策:
メンテナンスを行っても、劣化が進行した場合は交換が必要 になります。以下の判断基準を参考にしましょう。
✅ 腐食が進行し、構造強度が50%以上低下している
✅ ひび割れが拡大し、補修では強度が回復しない
✅ 金属疲労による亀裂が複数箇所で発生している
✅ 法定点検で「交換推奨」と診断された
✅ 設備の寿命を超え、安全基準を満たさなくなった
交換目安(業界別)
溶接構造物の寿命を延ばすためには、以下の対策が有効です。
✅ 定期点検を実施し、小さな異常でも早めに補修する
✅ 防錆処理(塗装・メッキ・コーティング)を適切に施す
✅ 荷重のかかる部分を補強し、応力を分散する設計に変更する
✅ 腐食の進行を抑えるため、湿気対策・排水設備を整備する
✅ 高耐久性材料(ステンレス・耐候性鋼)を使用する
溶接構造物は、定期的なメンテナンスと適切な交換判断によって、安全性を確保し、長期間使用することが可能 です。
✅ 劣化の兆候(腐食・ひび割れ・金属疲労)を早期発見する
✅ 適切な補修を行い、大規模な交換を防ぐ
✅ 交換が必要なタイミングを見極め、安全性を確保する
溶接工事を行った後も、適切な管理を続けることで、耐久性の高い溶接構造を維持しましょう!
お問い合わせはお気軽に♪
皆さんこんにちは!
合同会社Levi’s商会、更新担当の中西です。
さて
~耐久性~
ということで、溶接方法ごとの耐久性に着目し、特徴や適用例、長寿命化のためのポイントについて詳しく解説 していきます♪
溶接は、金属同士を接合する重要な技術であり、建築・造船・自動車・機械製造・配管など、さまざまな産業で活用 されています。溶接の品質は、接合部分の強度や耐久性に直接影響を与えるため、用途に適した溶接方法を選ぶことが不可欠 です。
しかし、溶接の方法によって耐久性が異なることを知っていますか?
溶接にはアーク溶接・TIG溶接・MIG溶接・レーザー溶接・スポット溶接などさまざまな工法 があり、それぞれの耐久性や用途が異なります。
溶接の耐久性は、以下の4つの要素によって左右されます。
溶接方法ごとに、接合強度・耐久性・耐食性が異なる ため、用途に応じた適切な工法を選ぶことが重要です。
鉄・ステンレス・アルミ・チタンなど、金属の種類によって溶接の強度や耐久性が変わる ため、適切な溶接技術が求められます。
溶接の品質が低いと、ひび割れ・溶接欠陥・応力集中による劣化 などの問題が発生し、耐久性が低下します。
屋外や海水環境、高温環境など、使用環境によっては腐食や劣化が進行しやすくなる ため、適切な保護処理が必要です。
耐久性:★★★☆☆(中程度)
特徴:屋外でも施工可能だが、強度はやや劣る
✅ メリット
❌ デメリット
➡ 適用例:建築工事、鉄骨構造物、橋梁、プラント工事
耐久性:★★★★★(非常に高い)
特徴:高品質な仕上がりで、耐食性・耐久性に優れる
✅ メリット
❌ デメリット
➡ 適用例:食品・医薬品工場の配管、高級自動車部品、航空宇宙産業、精密機器
耐久性:★★★★☆(高い)
特徴:スピードが速く、強度も高いが、屋外での使用には注意
✅ メリット
❌ デメリット
➡ 適用例:自動車のフレーム・ボディ、産業機械、鉄道車両、船舶
耐久性:★★★★★(非常に高い)
特徴:精密な溶接が可能で、ひずみが少なく高強度
✅ メリット
❌ デメリット
➡ 適用例:電子部品、医療機器、航空宇宙産業、半導体製造装置
耐久性:★★★☆☆(中程度)
特徴:薄板の接合に適し、大量生産に向いているが、耐久性は限定的
✅ メリット
❌ デメリット
➡ 適用例:自動車の車体、家電製品、薄板金属の接合
溶接の耐久性を向上させるためには、以下のポイントを押さえることが重要です。
✅ 適切な溶接方法を選択する
➡ 使用環境や求める強度に応じて、最適な工法を選ぶ
✅ 溶接部の前処理を丁寧に行う
➡ 母材の汚れや油分を除去し、溶接欠陥を防ぐ
✅ 適切な溶接条件(温度・速度・電流)を設定する
➡ 均一な溶接ビードを形成し、強度を高める
✅ 耐食処理や仕上げを行う
➡ ステンレス・アルミなどは、酸洗いや防錆処理を施す
溶接の耐久性は、使用する工法や環境、品質管理によって大きく異なります。
✅ 高強度が必要な場合は「TIG溶接」や「レーザー溶接」
✅ 生産性を重視するなら「MIG/MAG溶接」や「スポット溶接」
✅ 屋外での施工には「被覆アーク溶接」
適切な溶接方法を選び、適切な管理を行うことで、長期間使用できる高耐久な溶接構造を実現 しましょう!
お問い合わせはお気軽に♪