-
最近の投稿
アーカイブ
カテゴリー
投稿日カレンダー
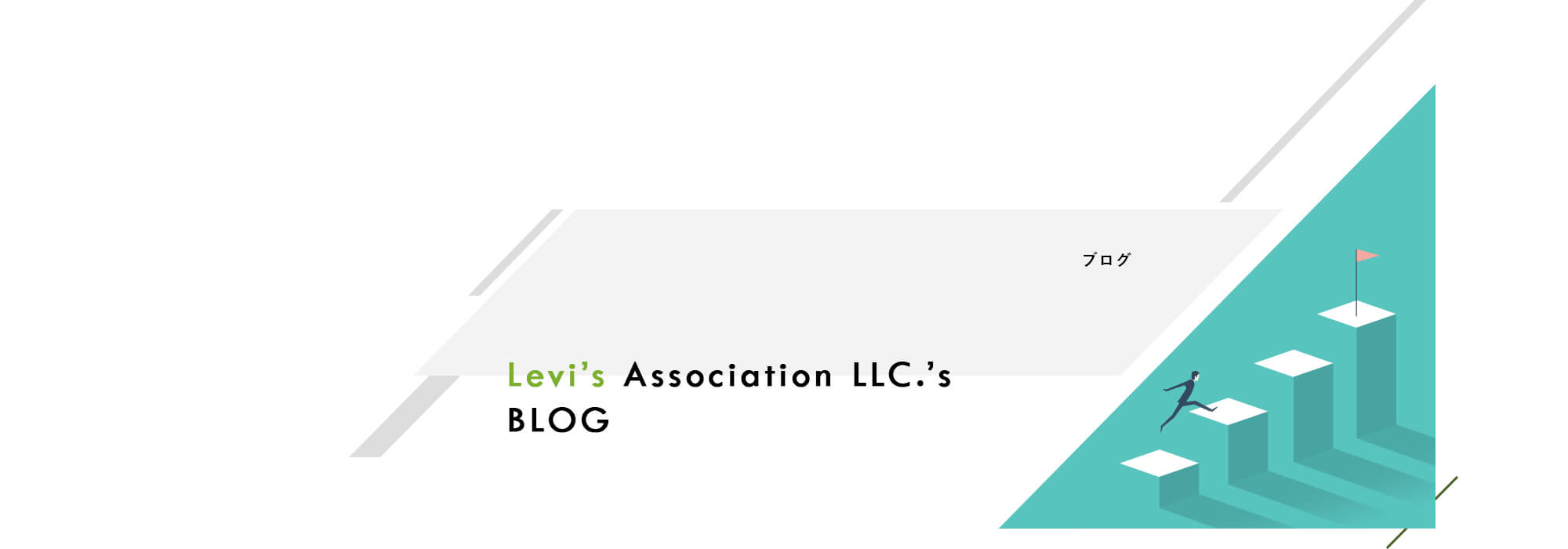
皆さんこんにちは!
合同会社Levi’s商会、更新担当の中西です。
~“強く・きれい・早い”~
「ビードが乗らない」「ヒケ・ブローホールが出る」「組立後に“曲がる”」——溶接の悩みは尽きません。
ここでは設計→開先→溶接条件→検査→歪み管理まで、現場ですぐ使える型をまとめました。
目次
軟鋼(SS材):
MIG/半自動(GMAW)が主力。屋外・下向以外はFCAWも強い。E7018/ER70S-6が定番。
ステンレス(SUS304/316):
**TIG(GTAW)**で清浄・薄板が得意。低入熱で焼け・歪みを抑える。
アルミ(5052/6061):
AC-TIG/Pulse MIG。酸化膜除去(ワイヤブラシ/ACバランス)と清浄な母材が命。
厚板・大入熱:
**SAW(サブマージアーク)**や多層盛り。予熱・パス間温度の管理が品質を左右。
屋内/屋外・板厚・姿勢・必要強度を軸に選定。**WPS(溶接施工要領書)**で前提を共有するのが第一歩。
開先角度・ルートギャップを図面で固定(例:V45°/ルート1.5mm等)。
面取り&脱脂:ミルスケール・油・水分は欠陥の原因。
仮付け:短・点数多めで歪みを抑制。対称配置が基本。
ルートフェイス:薄すぎると焼け落ち、厚すぎると未溶け込みになりやすい。
電圧・電流・送給はアーク長=一定を狙う。
**Stick-out(伸び)**は10〜15mm目安、角度は押し/引きでビード形状を使い分け。
パルスは薄板・隅肉の入熱低減に有効。
ガス:軟鋼はCO₂/混合ガス、SUS/AlはAr系。流量は風・ノズル径に合わせる。
ミニ試験(50×200mmの同条件3枚)でビード高さ・脚長・裏波を確認→WPSへ反映。
ブローホール(気孔):表面汚れ/湿気/ガス被覆不足 → 脱脂・乾燥・シールド強化
未溶け込み:低電流/速度過多/開先不良 → 入熱↑ or 速度↓、開先再調整
アンダーカット:電圧高すぎ/角度不良 → 電圧↓、トーチ角度見直し
割れ:高硬化・急冷・拘束 → 予熱・後熱・拘束緩和・低水素材
対称溶接(左右交互)
スキップ/バックステップ
短ビード分割(連続長を短く)
治具・拘束(でも過拘束に注意)
入熱管理(パス間温度・休止)
反り代の設計(先曲げ/先反り)
ピーニング/矯正は最後の手段
外観(VT):脚長・余盛・アンダーカット・欠陥有無。
PT/MT:表面・近表面の割れ検出。
UT/RT:内部欠陥の確認(厚板・重要部)。
記録:ヒート番号・ロット・WPS/パラメータ・検査結果を写真台帳で一元管理。
PPE:遮光面、難燃手袋・エプロン、皮ブーツ。
換気・集塵:ヒューム吸引・局排・屋外作業時の風向に配慮。
ボンベ:立てて固定、火気から距離。
火花飛散:養生シート/火花受け、火の元巡回(Fire Watch)。
清浄(両面脱脂+酸化皮膜除去)
最小入熱(電流低め・パルス活用)
トーチ角10–15°+短アーク、フィラーは一定リズムで送る
Before:連続長300mm一気盛り→**角度ズレ0.8°**発生
After:150mm×2スキップ+バックステップ+クランプ2点
結果:ズレ0.2°、仕上げ削り**▲40%**、タクトも短縮✨
溶接は**設計(WPS)×前処理(開先・清浄)×条件(入熱)×検査(記録)**の総合格闘技。
“強く・きれい・早い”は両立できます。現場に合う型を作って、繰り返し再現していきましょう。✨
お問い合わせはお気軽に♪
皆さんこんにちは!
合同会社Levi’s商会、更新担当の中西です。
~経済的役割~
現代社会において、目に見える建物や製品の裏側には、必ずと言っていいほど溶接の技術が存在しています。鉄やアルミなどの金属をつなぎ合わせ、強度・機能性・安全性を支える溶接技術は、建築・製造・エネルギー・交通インフラなど、さまざまな産業の基盤を形成しています。
溶接業が経済活動全体にどのように貢献しているのか、その役割と可能性について深く掘り下げます。
目次
溶接は、単なる“接合”作業ではなく、製品や構造物の寿命・品質・安全性を左右する極めて重要な工程です。
建設業(鉄骨建築、橋梁、高層ビルなど)
自動車産業(ボディ、シャーシ、バッテリーケースなど)
造船・鉄道・航空宇宙(精密で強度が求められる溶接)
プラント・エネルギー分野(原子力・火力・風力設備のパイプや機器)
製造業一般(産業機械、農業機械、家電製品など)
つまり、溶接業は「ものづくりの背骨」として、経済活動の幅広い分野を根底から支えています。
溶接業者は、建設会社・メーカー・ゼネコン・設計事務所などと密接に連携しながら仕事を行う業種であり、その存在は1次・2次・3次と広がる産業ピラミッドにおいて不可欠です。
地場の工務店や建築業者と協働することで、地域経済の循環を促進
地元の技能者・職人の雇用を創出し、若年層の雇用機会を提供
地域密着型の製造・修理・メンテナンス対応により中小企業の存続を支援
とくに中小企業や個人事業主が多い分野であるため、地方都市や工業地帯の経済安定にも大きな役割を果たしています。
近年、溶接業は単なる下請け構造から脱し、高度な技能・品質管理・設計力を持つことで「高付加価値産業」として認知されつつあります。
精密溶接技術による医療機器・半導体製造装置の製造
溶接ロボットやAI技術との融合による自動化と生産性向上
アートや家具業界への展開によるBtoC市場の開拓
これにより、高単価受注や技術輸出の機会が増え、日本の製造業の競争力維持にも貢献しています。
溶接業は技能職の代表格であり、学歴や資格よりも技術と経験が重視される分野です。そのため、多様な背景を持つ人々に就業機会を提供しています。
技能実習制度による外国人材の受け入れ
若手の職業訓練校からの採用
女性や高齢者の活躍の場の拡大
また、ベテラン職人によるOJT(オン・ザ・ジョブ・トレーニング)を通じた技術継承の文化が根付きやすく、長期的な人材育成の面でも経済を支える存在です。
日本国内では、高度経済成長期に建設されたインフラの老朽化が急速に進行しています。橋梁、トンネル、タンク、パイプラインなどの補修・補強には、熟練溶接工の技術が欠かせません。
インフラメンテナンス市場の拡大(将来数兆円規模)
補修対応による公共投資の効率化・延命
安全性を確保することで経済活動の継続性を保証
このように、溶接業は見えないところで日本社会の安全と経済を守る産業として、ますますその重要性を増しています。
表には出にくいながらも、溶接業は広範な産業の接合点であり、技術・雇用・地域経済・社会インフラに直結した存在です。多様化・高度化・専門化が進む中で、溶接業は単なる作業者ではなく、日本の製造力・安全性・経済的持続性を支えるエンジンといえるでしょう。
これからの時代、技術力を武器に新たな価値を創出する溶接業の活躍に、ますます注目が集まるはずです。
お問い合わせはお気軽に♪
皆さんこんにちは!
合同会社Levi’s商会、更新担当の中西です。
~多様化~
溶接業は、かつては鉄骨構造物や造船、建設現場での金属接合に特化した分野と見なされていました。しかし近年、この業界は技術革新と社会的ニーズの変化を受けて、多様化の道を歩んでいます。従来の「つなぐ」仕事にとどまらず、より高度で幅広い付加価値を創出する産業へと進化しつつあるのです。
目次
溶接と聞くと鉄やステンレスなどの一般的な金属を想像しがちですが、現代の製造業や建築業では、アルミニウム・チタン・炭素繊維強化プラスチック(CFRP)など、さまざまな素材が使用されており、それぞれに適した溶接技術が必要です。
レーザー溶接や電子ビーム溶接などの高精度溶接技術
**摩擦攪拌溶接(FSW)**によるアルミニウム構造の接合
医療機器分野における超音波溶接
これらの技術の導入により、溶接業は工業分野に限らず、医療・航空宇宙・自動車・エレクトロニクスといった最先端分野へと展開しています。
現場での施工溶接のみならず、溶接業は設計段階からの参画やメンテナンス対応、補修溶接、検査・非破壊検査などにも広がっています。
また、近年ではアート溶接やDIY市場にも注目が集まっています。インテリア製品や店舗什器、ガーデンアイテムなどを手がける「クラフト系溶接職人」も増えており、BtoBだけでなくBtoCのビジネスチャンスも拡大しています。
デジタル技術の進展により、図面共有や作業管理がクラウドベースで行えるようになったことで、個人事業主の溶接工やスモールビジネスとしての開業も現実的になっています。
また、副業として溶接スキルを活かす人や、溶接×YouTube・SNSでの発信を通じて自分の技術を収益化する動きもあり、職人としての自由度が高まりつつあります。
従来、男性中心であった溶接業界にも変化の兆しが見えています。女性溶接士が増加し、細やかな作業が求められる精密機器の溶接などで活躍するケースも目立ちます。
さらに、技能実習制度や特定技能制度により、外国人労働者の受け入れが拡大。異文化と技術の融合が、新たな発展の糸口となっています。また、高校や専門学校での技術教育の充実により、若年層の技能職への関心も高まりつつあります。
環境規制の強化や、労働安全衛生への関心の高まりに伴い、溶接業界でも排煙対策・作業環境の可視化・AIによる安全監視といった新たな取り組みが求められています。
また、ロボット溶接やAI制御による自動化技術の導入により、従来の危険作業からの脱却が進み、作業者の負担軽減や品質の均一化にも貢献しています。
溶接業の多様化は、単に作業の幅を広げることにとどまらず、新たな産業連携の創出、人材の活性化、地域経済の発展にもつながっています。職人の技と先端技術の融合が進む今、溶接業は「縁の下の力持ち」から、「未来をつくる主役」へと変貌を遂げているのです。
お問い合わせはお気軽に♪
皆さんこんにちは!
合同会社Levi’s商会、更新担当の中西です。
目次
前回は溶接業の“やりがい”についてお話ししましたが、今回はその延長線として、「溶接業の魅力」に焦点を当ててみたいと思います。
溶接は、建築や製造業のどんな分野でも必要不可欠。
国家資格(溶接技能者評価試験、JIS Z 3801など)を取得すれば、全国どこでも働ける職能となります。
鉄骨建方の現場溶接
配管の突合せ溶接
製缶工場でのTIG溶接
船舶や大型機械の製造
経験と資格を重ねれば、高単価の現場や海外プロジェクトにも参加でき、まさに“技術がキャリアになる”職業です。
溶接業界では、経験年数が浅くても「実力」が評価されやすい世界です。
20代でも1日2万円超の現場あり
危険物溶接、狭小空間作業などでは手当増
資格取得により日当・月収がすぐにアップ
肉体的な厳しさはありますが、やればやるほど評価と報酬がついてくるのが、この仕事のリアルな魅力です。
溶接は世界共通の技術です。
ISO規格・ASME・AWSなどの国際資格を取得すれば、造船、エネルギー、インフラ工事などの国際現場でも即戦力になります。
海外プラント工事の日本人溶接職人
海外研修や技能実習での外国人との交流
翻訳を超えた「技術の共通言語」
つまり、溶接は“世界で通用する日本の匠”を目指せる道でもあります。
AIやロボットが進化しても、全自動では難しい“感覚的調整”が必要な溶接は依然として人間の仕事です。
薄板と厚板の微妙な熱加減
鉄が反るクセを見越した溶け込み
微妙な手の角度とスピード制御
これらはまさに「職人芸の世界」。
機械化の時代だからこそ、“人にしかできない技術”に価値が高まると言えるでしょう。
溶接は「技術職」であると同時に、「美しさを追求する職人技」でもあります。
均一なビード幅
表面の滑らかさ
スラグ除去後の美しい仕上がり
自分の技術が“美しさ”として形に残る――
これは芸術家や職人に共通する、深い充実感につながります。
溶接は、どこにでも通用し、誰かの暮らしや社会インフラを支え、
しかも一生ものの技術とやりがいを得られる職業です。
技術を極めたい人に
手に職をつけたい人に
地道でも誇りある仕事を求める人に
――溶接業は、まさに“技術で生きていく”という選択肢を後押ししてくれる仕事です。
あなたも、金属を、社会を、そして未来を「つなぐ」職人になってみませんか?
次回もお楽しみに!
お問い合わせはお気軽に♪
皆さんこんにちは!
合同会社Levi’s商会、更新担当の中西です。
目次
今回は、あらゆる建築・製造・インフラの現場で必要とされる「溶接業」に焦点を当て、**その“やりがい”**について現場のリアルな視点から深掘りしていきます。
溶接は、金属同士を熱や圧力、またはそれらの組み合わせによって接合する技術です。
使われる場面は実に多岐にわたります:
建築鉄骨の接合
橋梁・高速道路の鋼構造部
造船・航空機の製造
工場プラントや配管設備
自動車・鉄道・機械部品
そのどれもが、“接合部の強度=構造物の安全”に直結しています。つまり、溶接が社会の基盤を支えているのです。
溶接は、配線やコンクリート工事と異なり、“自分の手で直接つくる”仕事です。
溶接ビード(接合部の跡)は職人の腕前がはっきりと出る部分。整ったビード、ピタリと収まる接合面、それがずっと残ります。
「この橋は自分が溶接したんだ」
「この工場の骨格を俺がつなげたんだ」
――こうした実感こそが、何にも代えがたいやりがいになります。
溶接には種類があります:
アーク溶接
半自動溶接(MAG/MIG)
TIG溶接
プラズマ溶接
ロボット溶接のオペレーション
初心者でも基礎から学べますが、突き詰めれば突き詰めるほど、まるで武道や芸術のように奥が深い世界です。
材料の種類
板厚や母材の組み合わせ
溶接姿勢(下向き、横向き、立向き、仰向き…)
毎回が異なる条件下での勝負。だからこそ、「昨日より上手くなれた」ことを実感できる仕事でもあります。
ビルや橋、船、発電所、配管…
どれか一つでも溶接が崩れれば、事故や人命に関わる重大事態につながりかねません。
だからこそ、溶接業は「信頼される技術者」でなければならない。
安全を守る、信頼に応える、誰かの命を支える――
この責任と誇りこそが、やりがいに直結します。
派手な仕事ではありません。
でも、建築現場の鉄骨も、配管工事の継手も、工場の装置も、すべて溶接という“見えないチカラ”がなければ成り立たない。
目立たないからこそ重要。
“地味だけど、超重要”。――これが溶接職のやりがいなのです。
溶接という技術は、単なる金属加工ではありません。
人と人の信頼、安全と未来、そして技術の継承を“つなぐ”仕事です。
目の前の鉄と真剣に向き合うことで、社会の大動脈を築く――
そんなやりがいある現場が、今日もあなたを待っています。
次回もお楽しみに!
お問い合わせはお気軽に♪
皆さんこんにちは!
合同会社Levi’s商会、更新担当の中西です。
目次
前回に続いて、今回は「溶接業の未来」について一般的な市場での動向を掘り下げます。
技術の進化・労働環境の改善・人材育成…さまざまな視点から、これからの溶接業界がどう変わっていくのかを見ていきましょう。
すでに多くの製造現場では「ロボット溶接」が導入されています。
自動車のライン溶接
船舶・鉄骨の大型自動溶接
ファイバーレーザーによる精密溶接
こうした技術によって、品質の均一化・作業スピードの向上・安全性の確保が進んでいます。
ただし、すべての現場が自動化できるわけではなく、
配管内部や狭い場所
現場ごとに仕様が異なる構造物
修理・改修工事などのイレギュラー作業
では、今後も人の手による熟練技術が不可欠です。
新しい現場管理では、デジタル技術が活躍しています。
溶接部の温度・時間・電流管理のデジタル化
品質記録の自動保存・トレーサビリティ
現場作業をクラウドで遠隔モニタリング
これにより、施工管理の精度と効率が大幅に向上しています。
従来は「現場で見て覚える」スタイルが主流だった溶接技能ですが、今では
VRによる溶接体験トレーニング
シミュレーターでの練習環境
動画による技術共有・講座配信
など、新しい教育手法が登場し、若手育成がしやすい環境になりつつあります。
溶接においても、「脱炭素」や「省資源」が求められる時代です。
エネルギー効率の高い機器への更新
無煙・低臭ガスの使用推進
リサイクル材への対応技術
など、環境と共存できる技術革新が、今後さらに重要視されるでしょう。
これからの溶接業界は、単なる職人技の世界から、
**技術・デジタル・持続可能性を融合した「スマートな技能職」**へと進化していきます。
熟練の手仕事と、ロボット・ITが共存することで、
「安全・効率・高品質」な溶接の新時代がやってくるのです。
次回もお楽しみに!
お問い合わせはお気軽に♪
皆さんこんにちは!
合同会社Levi’s商会、更新担当の中西です。
目次
今回は、鉄骨や配管、建設、造船、自動車など…さまざまな産業を支える「溶接業」の現場環境について一般的な市場での動向をご紹介します。
火花を飛ばしながら金属同士を結合するこの仕事、見た目の派手さ以上に、繊細な技術と体力が求められる世界なのです。
溶接とは、金属同士を接合する技術であり、主に以下のような分野で活躍しています。
鉄骨建築(ビル・橋梁)
配管・タンク(プラント・製油所)
造船・船舶構造物
自動車・鉄道車両・航空機の製造
精密機械や家具などの部品加工
つまり、溶接はあらゆる「モノづくり」の根幹を担う重要な工程なのです。
現場では、さまざまな環境要因が作業者の負担となります。
火花やアーク熱によって、作業空間は40〜50℃にもなることがあります。
特に夏場の屋内現場や配管内部では、熱中症リスクが非常に高いです。
タンク内部や高層鉄骨の上など、狭くて危険な場所での作業が多く、動きの自由がききません。
防護面をつけたままの作業や、仰向け・うつ伏せでの長時間作業も珍しくなく、身体的負担が大きいです。
溶接中は金属が2000℃近くまで加熱されるため、火傷や引火事故の危険性が常にあります。
また、金属から出る煙やガスは長期的な健康リスクも。
溶接は危険と隣り合わせだからこそ、安全装備の徹底が不可欠です。
遮光面・溶接ゴーグル
難燃性の作業着と手袋
熱中症対策の送風ベスト
換気と排煙設備の整備
また、現場ごとの**作業前ミーティング(KY活動)**や、定期的な健康診断・資格更新も大切なルールです。
溶接業界では、「人手不足」と「高齢化」が深刻です。
高温・重作業で若者が敬遠
作業は経験による職人技が必要で、即戦力化が難しい
技術継承の機会が減少し、ベテランに業務が集中
このままでは「技術の空白世代」が生まれてしまう可能性もあるのです。
一方で、溶接は国家資格や専門性が求められる「技能職」の代表格でもあります。
一生モノのスキルが身につく
高度な資格を取得すれば高収入・海外派遣のチャンスも
熟練者は企業から引っ張りだこ
「モノづくりが好き」「現場で働くのが性に合う」という人にとっては、非常にやりがいのある職業です。
溶接の現場は、暑く・重く・危険がつきまとう厳しい環境です。
しかし、そこには鉄と火を操る職人たちの矜持があり、建設や製造という大きな産業の土台を支えています。
次回は、そんな溶接業がこれからどんな「未来」を迎えていくのかを展望します。
次回もお楽しみに!
お問い合わせはお気軽に♪
皆さんこんにちは!
合同会社Levi’s商会、更新担当の中西です。
さて
~設計~
ということで、溶接業における設計の基本的な考え方から、実務上の重要ポイントまでを、深く・丁寧に解説します。
強度・精度・安全性を支える“目に見えない技術設計”の世界
溶接とは、「金属と金属を一体化させる」ための最も重要な接合技術。
建築構造物、橋梁、配管、車両、船舶、圧力容器など、あらゆる分野で利用されており、
その信頼性と安全性は、溶接設計の良し悪しに大きく依存しています。
目次
溶接設計とは、溶接を含む構造物・製品に対して、次のような観点から計画的に仕様を決める技術的プロセスです。
必要な強度・剛性を確保する
製造・施工が容易で、コストが最適化されるようにする
熱変形や応力集中を最小限に抑える
安全性・品質・耐久性を長期間保つ
📌 溶接設計は、“設計図に現れにくいが製品寿命を左右する”技術領域とも言えます。
「設計者の意図」と「現場の溶接」が噛み合わなければ意味がない
項目 | 内容 |
---|---|
接合部の配置 | 応力が集中する箇所を避ける(角・端部を避ける) |
溶接部の方向 | 引張・せん断・曲げ力に対して最も強い接合方向を選定 |
継手の種類 | 突合せ継手/隅肉継手の使い分け(強度・施工性に影響) |
板厚の調整 | 異なる板厚同士の溶接ではスカラップ処理が必要 |
開先形状 | JIS Z 3021などに基づき、適切な角度・深さ・寸法を設計 |
📌 「設計上はOK」でも、「実際には溶接できない・歪む」というケースも多いため、現場との連携が重要です。
材料・構造・コスト・作業環境に応じた“最適な工法”を設計段階で決める
溶接設計では、使用する溶接法の選定も非常に重要です。
溶接法 | 特徴 | 主な用途 |
---|---|---|
アーク溶接(被覆アーク) | 手軽・汎用性高い | 鉄骨・建築構造物 |
TIG溶接 | 高精度・クリーン | ステンレス・アルミ配管 |
MAG/MIG溶接 | 半自動・連続作業向き | 自動車部品・製缶 |
スポット溶接 | 高速・省力 | 薄板・自動車・家電製品 |
サブマージアーク溶接(SAW) | 高厚板に対応・自動化向き | 圧力容器・橋梁 |
📌 設計者は「どの工法が現場に最も適し、品質・コスト・安全性を両立できるか」を見極める必要があります。
“熱”がもたらす見えないリスクと向き合う
溶接は「熱加工」であり、高温による金属の膨張→収縮=歪みの発生がつきものです。
対象部材の拘束条件の緩和(可動部・スリットの設置など)
溶接順序や位置の工夫(対称溶接・点付け→本付け)
組立時のプレストレス設計(意図的な逆歪みなど)
余盛寸法の適正化(溶着量の過剰は歪みの原因に)
📌 熱による歪み対策は、「施工後の補修では遅すぎる」ため、設計段階での想定が極めて重要です。
壊れない構造のための「計算」と「感覚」
静荷重(自重、常時荷重)
動荷重(風圧、地震、振動)
局部応力(ボルト・脚部支持点)
応力集中部を避ける接合位置選定
応力方向に沿った溶接(せん断応力に強い配置)
部材厚さと溶接サイズのバランス
📌 JIS Z 3001「溶接構造設計標準」や建築基準法、道路橋示方書などの法令・基準に基づいた設計が必要です。
設計者が意図しても、現場に正確に伝わらなければ意味がありません。
項目 | 内容 |
---|---|
溶接記号 | JIS Z 3021に準拠(突合せ、隅肉、フルペネなど) |
寸法指定 | 開先角度、余盛寸法、溶接長、ピッチ |
工法指定 | TIG/MAGなどの明示(必要に応じて) |
補足情報 | 熱処理条件、溶接順序、支持方法などの注意書き |
📌 溶接記号の読み間違いが現場トラブルの原因となるため、記載はシンプルかつ明確に。
溶接は、一見単純な接合作業に見えますが、
その背後には、熱・力・材料・環境といった複雑な要素の融合設計があります。
✔ 強度・剛性を保つ接合方法の選定
✔ 熱影響による歪みを防ぐ工夫
✔ 作業性とコストを見据えた最適設計
✔ 安全性と保守性を意識した構造配置
それら一つひとつが、製品の品質と現場の信頼につながっています。
設計段階でどれだけ先を見据えられるか。
それが、良い製品・安全な構造物を生み出す「設計者の力量」なのです。
カテゴリ | 確認項目 |
---|---|
接合部設計 | 応力方向、継手位置、開先形状、板厚対応 |
溶接法選定 | 材料適合性、作業環境、コスト、品質要求 |
歪み対策 | 溶接順序、補強部設計、対称配置 |
応力解析 | 荷重計算、疲労対策、冗長設計の有無 |
図面記載 | JIS記号、寸法、溶接長、注意書きの明記 |
お問い合わせはお気軽に♪
皆さんこんにちは!
合同会社Levi’s商会、更新担当の中西です。
さて
~確認事項~
ということで、今回は、溶接業における事前確認事項を、実務目線で深く解説いたします。
安全・品質・効率を守るための“段取り前の段取り”
溶接は、製造業や建設業において「構造を支える」重要な工程です。
鉄骨や配管、橋梁、船舶、機械フレームなど、あらゆる分野で使用されており、
一つの不良が重大な事故や大規模な手戻りにつながる可能性もあります。
だからこそ、溶接作業においては、「作業前の確認」が極めて重要です。
目次
すべては「正しく読む」ことから始まる
溶接作業の第一歩は、設計図や溶接指示図を正確に読み解くことです。
項目 | 確認内容 |
---|---|
溶接記号 | 種類(突合せ/隅肉など)、サイズ、長さ、角度 |
溶接部位 | 部材の取り合い位置、交差点、継手の種類 |
材質情報 | 母材の種類と強度(SS400、SUS304等) |
溶接方法 | アーク溶接/TIG/MAG/スポット等の指定 |
溶接順序・工程 | 歪み防止のための指定順序の有無 |
📌 「勝手な自己判断」で施工すると、強度不足・歪み・クレームの原因になります。
適材適所を守らないと、構造不良につながる
材質、板厚、表面のサビ・油・汚れの除去状況
異材溶接(例:鉄とステンレス)時の注意点
材料 | 確認事項 |
---|---|
溶接棒・ワイヤ | 材質の適合、保管状態、ロット管理 |
保護ガス | 種類(CO₂/Ar混合)、流量、ボンベ残量 |
フラックス(被覆材) | 湿気による性能低下がないか |
乾燥処理 | 低水素系電極は事前の乾燥が必須(300〜400℃) |
📌 材料が正しくても、管理が甘いと品質不良が発生します。事前点検は怠らずに。
人命を守るための“必須条件”
溶接作業には、高熱・強光・火花・有毒ガスといった多くの危険要素が含まれます。
項目 | 内容 |
---|---|
火災防止 | 可燃物の撤去、消火器・水バケツの設置 |
換気設備 | 排気装置・フードの稼働確認(ヒューム対策) |
保護具 | 溶接面、革手袋、防炎服、安全靴、耳栓など |
アース接続 | 接地状態の確認と漏電防止 |
足場・作業姿勢 | 高所作業時の墜落防止、安定した体勢確保 |
📌 現場での事故の多くは、「当たり前の確認を怠った」ことが原因です。
施工精度と安全性の両方に直結する工程
設備 | 点検内容 |
---|---|
溶接機本体 | 通電、表示パネル、異音・異臭の有無 |
ケーブル類 | 断線・焼損・接触不良 |
トーチ・ホルダ | 消耗品の状態、ノズルの詰まり |
ガス調整器 | 圧力計の動作確認、漏れの有無 |
グラインダー・ケレン機 | 回転ブレ・砥石の摩耗状態 |
📌 機器トラブルによる作業中断は、生産性だけでなく安全リスクも高めます。
誰が作業するかで、仕上がりは大きく変わる
溶接作業には、資格が必要な作業と、誰でもできる作業があります。
作業者の溶接技能資格(JIS Z 3801など)の有無
指定された施工方法に対応した資格範囲内か
特定建設業ではWES、AW検定、ボイラー溶接士等の資格証明の提出が必要なケースあり
📌 無資格者の施工は、重大事故や元請けからの指導対象になることも。
品質トラブルを未然に防ぐための「管理の目」
事前に品質管理・工程管理のルールを確認し、現場での迷いや属人的判断をなくします。
項目 | 内容 |
---|---|
WPS(溶接施工要領書) | 許容電流・速度・前処理・後処理が定義されているか |
PQR(溶接施工試験記録) | 検査結果の記録とトレーサビリティの確保 |
外観検査・寸法検査 | 作業後に即チェックできる体制があるか |
非破壊検査(RT/UT/MT/PT) | 必要な検査項目と実施手配は済んでいるか |
📌 検査体制は、顧客・元請けからの信頼に直結します。準備は万全に。
溶接作業においては、「実際の作業時間」よりも、事前準備や確認作業の質が最終結果を左右します。
✔ 図面と仕様の確認
✔ 材料と母材の適合性
✔ 作業環境と安全対策の徹底
✔ 機器点検と技能の確認
✔ 品質検査の体制構築
これらを抜きにした「いきなり施工」は、事故・不良・やり直し・信用喪失の元です。
溶接は、“火花の裏に設計と管理がある”
そのことを、すべての技術者が忘れてはならないポイントです。
分類 | チェック内容 |
---|---|
図面 | 溶接記号、位置、順序、材質の読み取り |
材料 | 溶接棒/ガス/母材の適合、保管状態 |
安全 | 火災対策、換気、保護具、足場確認 |
設備 | 溶接機・トーチ・ガス系統の点検 |
人材 | 資格者の配置、技能証明、健康状態 |
品質管理 | WPS・PQR・検査手配・測定機器準備 |
お問い合わせはお気軽に♪
皆さんこんにちは!
合同会社Levi’s商会、更新担当の中西です。
さて
~メンテナンスと交換時期~
ということで、溶接構造物のメンテナンス方法・交換が必要となる劣化の兆候・長持ちさせるポイントについて詳しく解説 します♪
溶接工事で作られた構造物や設備は、耐久性が高く、長期間使用できる ことが特徴ですが、定期的なメンテナンスを行わなければ劣化が進行し、安全性が低下するリスクがあります。
また、溶接部に発生するひび割れ・腐食・応力集中による金属疲労 などの問題は、放置すると重大な事故につながる可能性があります。
では、溶接物の寿命を延ばし、安全に使用するためには、どのようなメンテナンスが必要なのでしょうか?また、交換時期はどのように判断すればよいのでしょうか?
目次
溶接構造物は、建築物・橋梁・配管・機械部品・プラント設備など重要な役割を担っている ため、劣化を放置すると崩壊や破損のリスクが高まる 可能性があります。
✅ 例:橋梁の溶接部が腐食し、強度が低下すると、崩落事故につながる
✅ 例:プラント設備の配管が劣化すると、ガス漏れや爆発の原因になる
溶接部の劣化を早期に発見し、適切に補修すれば、大規模な修理や交換を防ぎ、コストを削減することが可能 です。
✅ 軽微なひび割れを補修せず放置すると、大きな亀裂に発展し、補修費用が数倍に増加する
✅ 定期メンテナンスを行えば、長期的に設備の寿命を延ばし、交換頻度を減らせる
溶接を用いた構造物は、定期的な検査が義務付けられているケースが多い です。例えば、
こうした法的な点検を怠ると、事故発生時に責任が問われることもあるため、適切なメンテナンスが不可欠 です。
溶接物の耐久性を損なう主な原因には、腐食・ひび割れ・金属疲労・応力集中 などがあります。これらの兆候を早期に発見することが重要です。
原因:
点検ポイント:
✅ サビが発生していないか?(特に溶接部周辺)
✅ 腐食による穴あきや表面の荒れがないか?
✅ 防錆塗装やメッキが剥がれていないか?
対策:
原因:
点検ポイント:
✅ 溶接部に細かいひび割れが発生していないか?
✅ 金属表面の異常(剥離や変色)がないか?
✅ 振動や荷重がかかる部分にひびが広がっていないか?
対策:
原因:
点検ポイント:
✅ 定期点検で溶接部の微細なひびを確認する
✅ 振動が多い部分のボルトや接合部の緩みをチェックする
対策:
メンテナンスを行っても、劣化が進行した場合は交換が必要 になります。以下の判断基準を参考にしましょう。
✅ 腐食が進行し、構造強度が50%以上低下している
✅ ひび割れが拡大し、補修では強度が回復しない
✅ 金属疲労による亀裂が複数箇所で発生している
✅ 法定点検で「交換推奨」と診断された
✅ 設備の寿命を超え、安全基準を満たさなくなった
交換目安(業界別)
溶接構造物の寿命を延ばすためには、以下の対策が有効です。
✅ 定期点検を実施し、小さな異常でも早めに補修する
✅ 防錆処理(塗装・メッキ・コーティング)を適切に施す
✅ 荷重のかかる部分を補強し、応力を分散する設計に変更する
✅ 腐食の進行を抑えるため、湿気対策・排水設備を整備する
✅ 高耐久性材料(ステンレス・耐候性鋼)を使用する
溶接構造物は、定期的なメンテナンスと適切な交換判断によって、安全性を確保し、長期間使用することが可能 です。
✅ 劣化の兆候(腐食・ひび割れ・金属疲労)を早期発見する
✅ 適切な補修を行い、大規模な交換を防ぐ
✅ 交換が必要なタイミングを見極め、安全性を確保する
溶接工事を行った後も、適切な管理を続けることで、耐久性の高い溶接構造を維持しましょう!
お問い合わせはお気軽に♪